Gear Coupling Reconditioning
The coupling reconditioning services provided by Xtek extend beyond just disassembling and re-assembling couplings with new parts. The services provided include: extensive analyses of each individual component, an understanding of the application, tracking of the couplings in-service and in inventory, monitoring the couplings performance, establishing appropriate campaign lengths, making recommendations to improve component performance and overall coupling assembly reliability, and evaluating operating costs associated with the couplings.
The Xtek Geared Spindle Coupling Reconditioning Cycle:
The Xtek coupling reconditioning cycle is a perfect example of the Xtek Continuous Improvement Principle. The intent of the coupling reconditioning program is to extend mill campaigns and lower operating costs.
- The coupling assemblies are received from the application and prepared for servicing and reconditioning.
- Technicians, inspectors, and engineers collect, evaluate and document all the data, and make recommendations for improvement.
- Manufacturing implements the recommended modifications using standard operating procedures and quality standards.
- The coupling assembly is certified for the next mill campaign.
The Xtek Coupling Reconditioning Program – Extending Mill Campaigns
Extending mill campaign lengths for geared spindle couplings is a principal operating goal for the rolling mills of today. Campaign lengths of 4-5 years between reconditioning periods is commonplace for Xtek reconditioned geared spindle couplings. Our application data shows that the average tonnage rolled by Xtek reconditioned geared spindle couplings in hot mill applications exceeds 7 million tons per campaign.
The Xtek Coupling Reconditioning Program – Lowering Operating Costs
Lowering the operating costs of geared spindle couplings is a principal goal for the maintenance teams of the rolling mills of today. As measured by: reconditioning cost / tons rolled, Xtek reconditioned geared spindle couplings operate at an average of less than $0.02 per ton. This is achieved by reconditioning spindles with high quality, technically advanced, replacement components, which in many cases can be re-used through several reconditioning cycles. In addition, the opportunities for upgrades to the couplings are examined through the extensive engineering evaluations that occur during every reconditioning cycle. By continually making upgrades and improvements to the couplings, Xtek can lower operating costs by reducing and sometimes eliminating recurring issues.
Coupling Reconditioning at Xtek – Cincinnati, USA
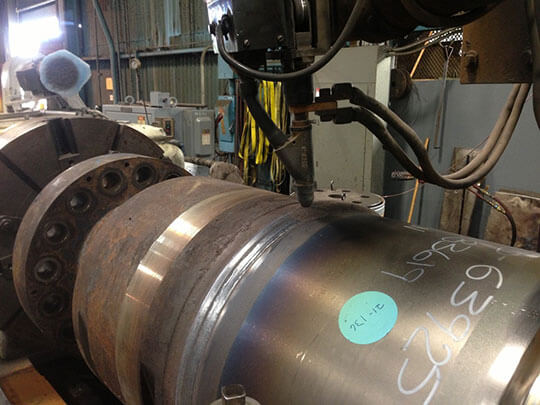
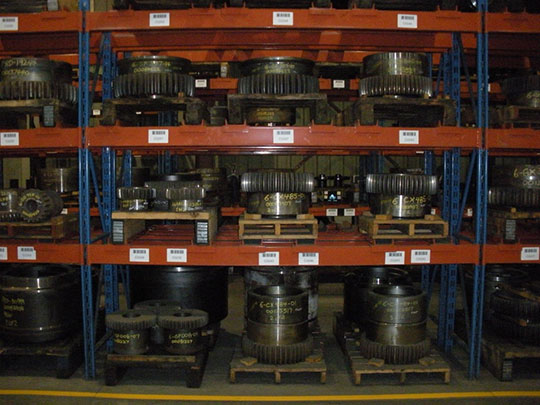
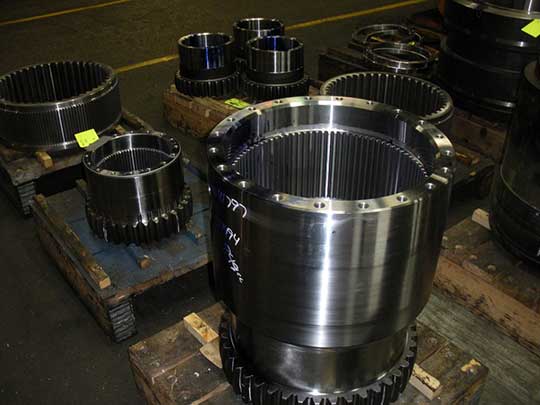
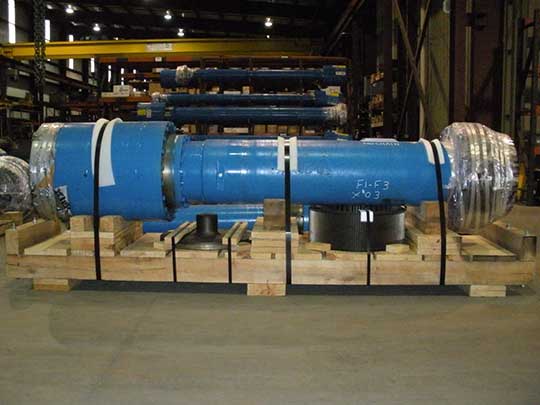
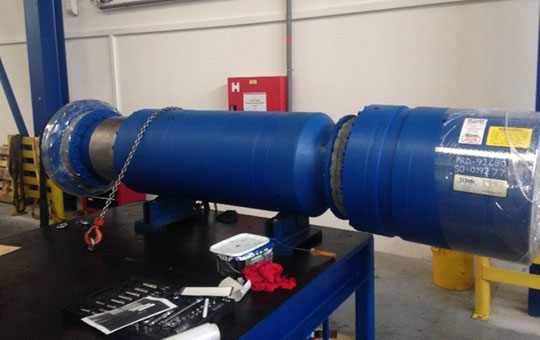
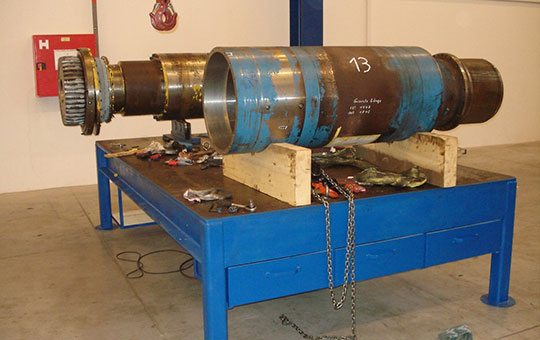