Improved Flange Characteristics
Survey results from AISE Crane Symposium
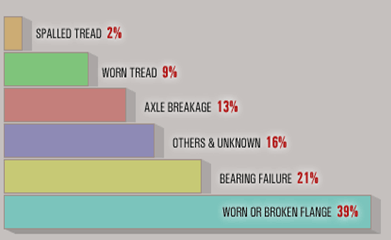
Almost 40 percent of all wheel replacements are due to excessive flange wear and breakage. And while it has been demonstrated that increasing surface hardness will improve wear resistance of the flange surface, a hardness that is too deep in the flange area will increase the probability of breakage, requiring the crane wheel to be replaced.
Just as a tough, ductile core beneath a hardened case helps to prevent spalling and pitting of the wheel tread, a ductile area backing up to the hardened case of a flange will absorb shocks generated by span misalignment and badly worn joints between rail sections. These shocks can stress wheel flanges to the point of catastrophic failure.
All Xtek contour case hardened crane wheels incorporate a differentially hardened flange designed to maintain critical ductile properties beneath the case. This valuable feature, which results from Xtek’s contour case hardening process, was developed over decades of metallurgical research and is vital to wheel flange toughness in service.
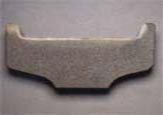
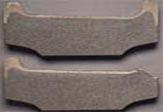
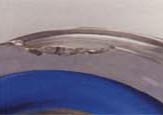
Contact us today to discuss your specific application and problem solving needs.